Innovating Solutions for PPE Sanitization
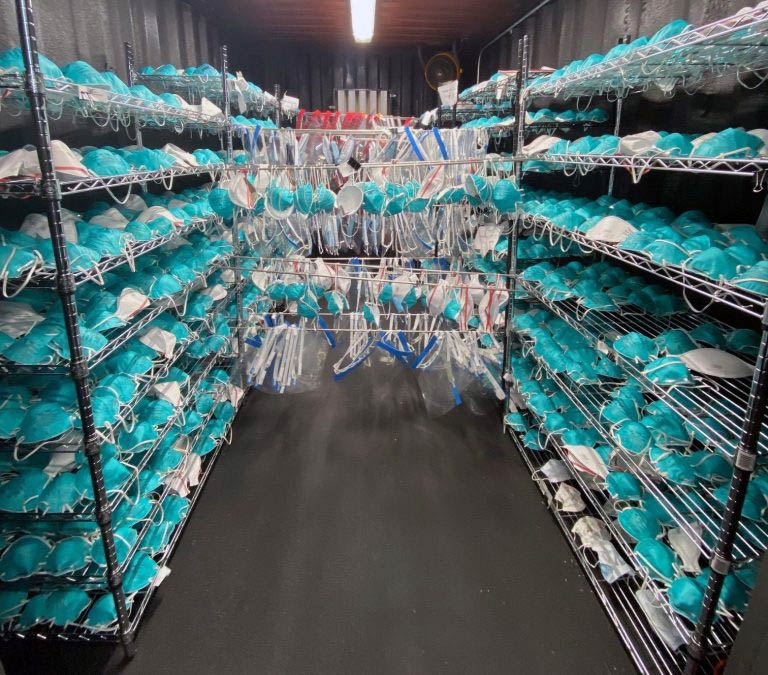
Introduction
Wolf Metals, a family-owned metal fabrication business in Columbus, Ohio, has consistently demonstrated its ability to pivot and innovate in response to challenges. During the COVID-19 pandemic, the company leveraged its expertise to address a critical need in the healthcare sector: sanitizing personal protective equipment (PPE).
The Challenge
Healthcare workers on the front lines of the pandemic faced an unprecedented shortage of PPE, such as masks and gowns. The reuse of PPE became necessary, but safe and effective sanitization methods were limited. Wolf Metals recognized the urgency of this issue and saw an opportunity to provide a solution that could help protect healthcare workers and support public health.
Innovative Solution
Wolf Metals collaborated with Battelle, a global research and development organization, to design and fabricate customized stainless-steel racks for a cutting-edge PPE decontamination system. These racks were a critical component of Battelle’s decontamination chambers, which used vaporized hydrogen peroxide to sanitize masks and other PPE items. The system enabled the reuse of PPE up to 20 times without compromising safety or functionality.
Scope of Work
Wolf Metals quickly mobilized its team and resources to meet Battelle’s needs. The project included:
- Design and Engineering: Collaborating with Battelle to refine the rack design to meet stringent safety and operational requirements.
- Fabrication: Using high-grade stainless steel to manufacture durable and reliable racks that could withstand repeated use and exposure to the decontamination process.
- Rapid Deployment: Scaling up production to deliver racks on a tight timeline, ensuring the decontamination systems could be deployed promptly to healthcare facilities nationwide.
Impact
The decontamination systems, equipped with Wolf Metals’ racks, played a pivotal role in alleviating the PPE shortage. These systems were deployed to hospitals and healthcare facilities across the United States, significantly reducing the burden on supply chains and protecting frontline workers.
Conclusion
Wolf Metals’ ability to adapt and deliver during a critical moment underscored its commitment to innovation, quality, and community support. By partnering with organizations like Battelle, the company demonstrated how local manufacturers could contribute to solving global challenges. Their efforts not only addressed an immediate public health need but also showcased the value of ingenuity and collaboration in the manufacturing industry.
For businesses seeking a reliable partner for custom fabrication projects, Wolf Metals serves as a prime example of dedication and capability in the face of complex challenges.
Our Capabilities in Action
Discover how our comprehensive capabilities have solved complex challenges for clients across various industries.
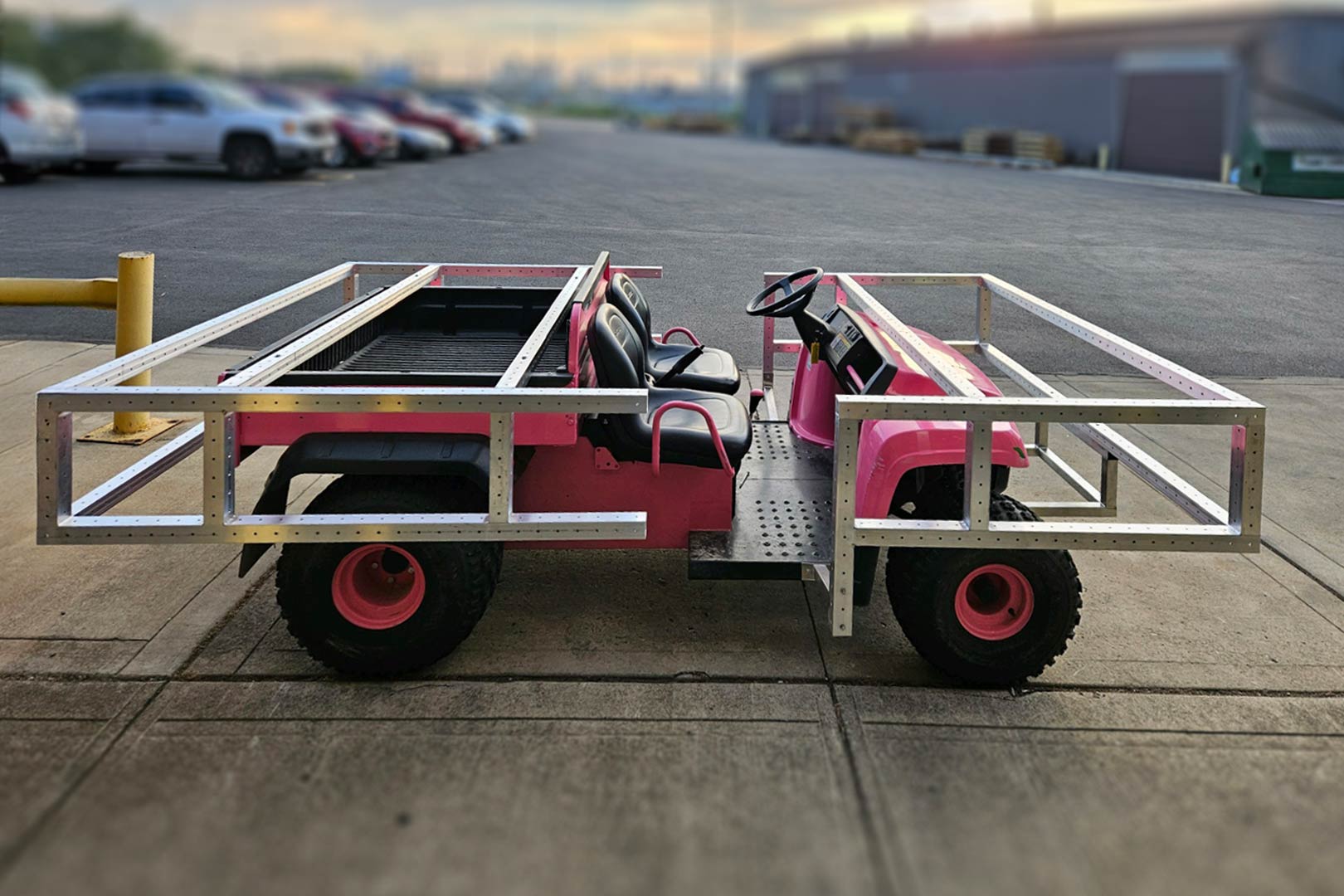
Case Study: Custom Exoskeleton Build for DTi Creative’s Marching Band Vehicles
Discover how Wolf Metals engineered a modular aluminum exoskeleton for DTi Creative, enabling marching bands to transform a John Deere Gator into unique performance vehicles like a Lunar Rover and a Pirate Ship. Learn more about this innovative fabrication solution.
Custom Fabrication for Any Scale Project
From one-of-a-kind specialty builds to high-volume corporate manufacturing, our team delivers precision and reliability at every stage. Request a quote today to discuss your project’s unique requirements.
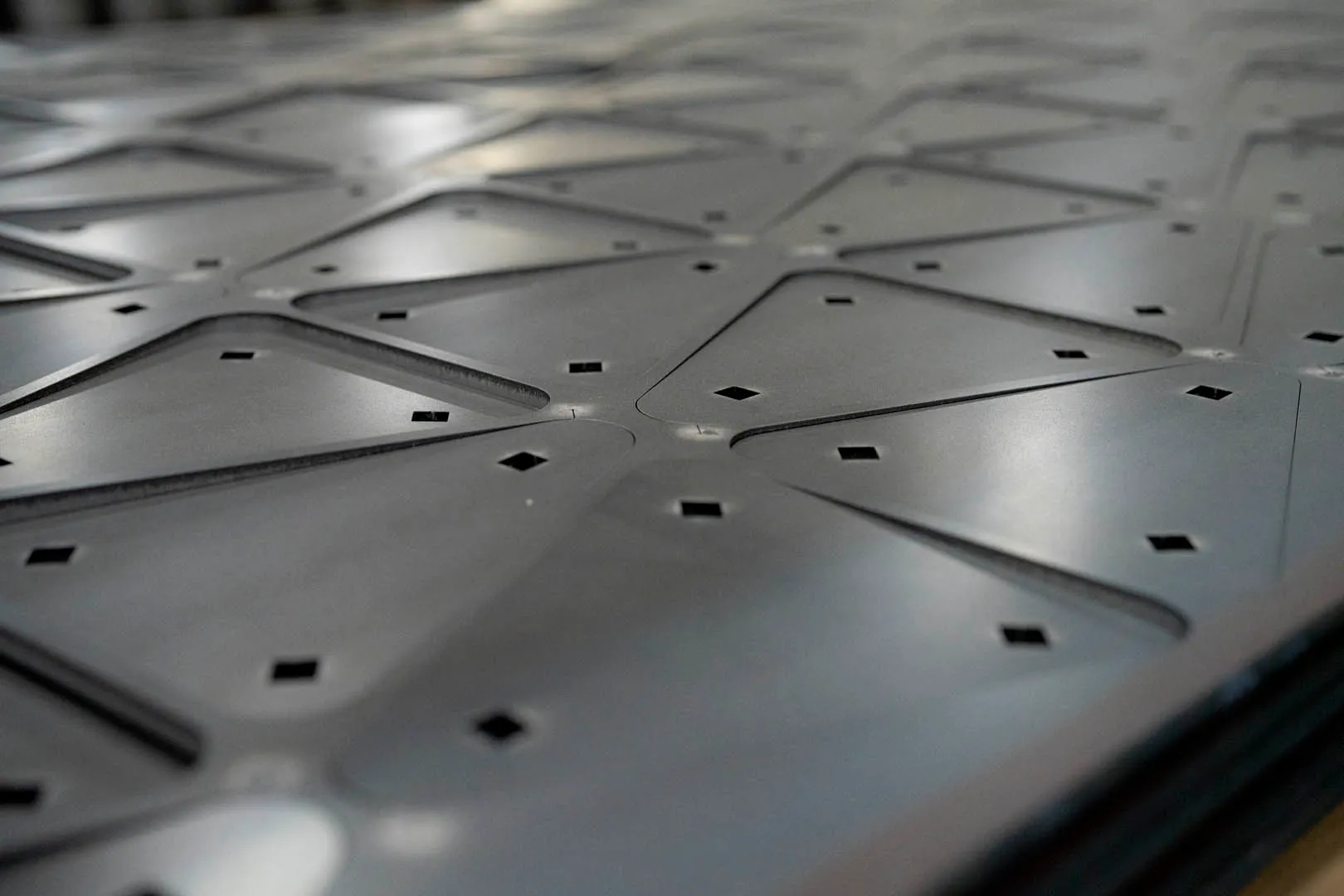